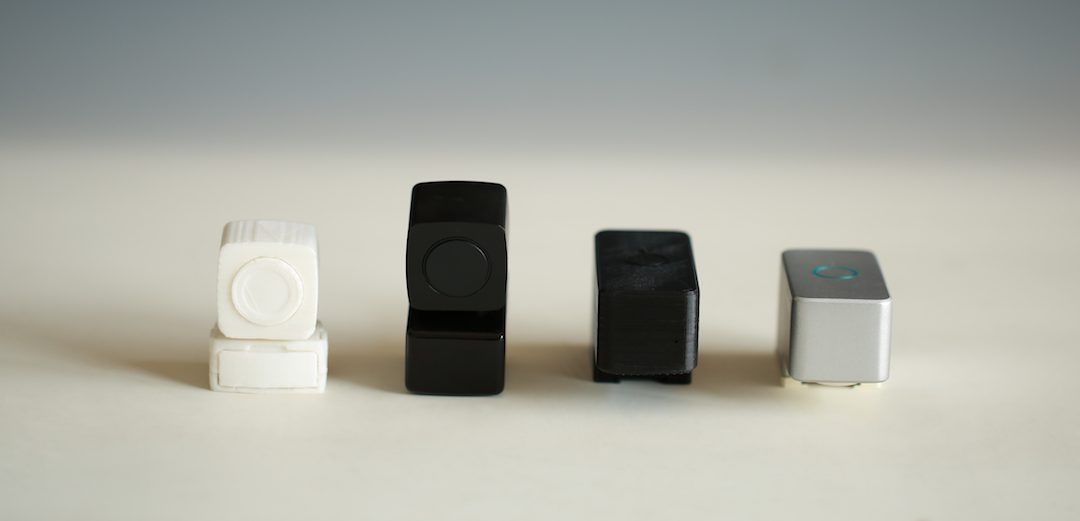
Evolution of Microbot Push. From the first 3D printed prototype to a functional pre-production prototype in six months.
The rapid evolution of Microbot Push started with a white 3D printed prototype that you see in the image above. It was the first time when our idea of universal home automation microbots materialised into something physical. In the next few paragraphs let us share how Microbot has evolved and why its shape is as it is now.
Lesson 1: standard batteries don’t fit consumer-microbotics
The first prototype comprised of two distinct parts. The smaller part at the bottom was a battery compartment, where intended to install standard commercially available batteries. The bigger section at its top contained a servo gear and pushing mechanism.
The concept appeared to be great on paper and in theory but in the real world nothing goes as planned. Standard batteries just didn’t last enough. They could keep Microbots operational for up to 3-4 months on a single charge, but we decided that this is way too short from a user’s perspective.
- Initial concept of Microbot Push.
- Battery had to go here.
Lesson 2: bigger isn’t always better
To compensate, we increased Microbots size so it could fit a larger battery. While the trick apparently worked and our tiny little helper could run for up to 6 months, we noticed another problem. Since Microbots became noticeably larger, their weight distribution also changed. One could think that this change of weight balance should not cause any considerable effect on such a small scale, but because Microbot’s body comprised of two distinct parts connected, the top part now would flex a lot when pushing a button. Some flexing will always occur, but too much of it is highly undesirable because a lot of energy that could go into pushing a button ends up entirely wasted.
Lesson 3: radically new products must be made from scratch
Of course, we were happy and hyped that our proof of concept worked in practise! Now we just had to fix a few small flaws. We found that identifying critical problems and then starting with a blank sheet of paper to solve them is the fasted and best approach to engineer a brand new product.
We took a blank sheet of paper and started with 3 “What ifs?”
- What if we design our batteries that work as much as we want them to work?
- What if we make our motor and gears to get the best performance for our special task?
- What if we package everything in a sleek body that will be the most potent form factor?
After multiple iterations, the third design was born. We made Microbot Push with custom batteries, entirely custom motor and a single body design to fit everything inside in the most elegant and also the most energy efficient way. Engineering team careful tested several 3D printed hand-finished versions of the new design and became confident with highly improved results. With a single body approach flexing was minimize and custom designed batteries could potentially run Microbot Push for up to 1.5 years. Though to be on the safe side, we are confident that you can use it for at least one year before you need to charge it again.
- Current concept of Microbot Push.
- Single body design is adjustable and optimized for most buttons.
- Will be available in white and grey.
Lesson 4: if you want results, iterate a lot
To wrap up, we are happy with the outcome we achieved only in six months. To move that fast we made a habit of iterating a lot. At least every one or two weeks we would have an iteration meeting where we would rethink everything that goes in and out the microbot. Yes, it’s hard but totally worth it. This way instead of staying stuck on details, we could achieve rapid progress with tangible, meaningful improvements over previous designs. Also, to see something improving and changing fast kept the whole team motivated and focused on getting it done quickly.